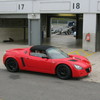
Elise Track Car Build Thread - Have You Lot See This One?
#441
Posted 09 December 2014 - 10:37 PM
#442
Posted 10 December 2014 - 12:04 AM
you can do much when your focused, tonight ive already transferred the indicators and tomorrow ill bond in the headlight brackets.
Got some material on order for my new splitter with full width diffusers, end plates and canards, the aim is to have the car complete before xmas, that way im going to be pounding around cadwell every track day i can book between january and april, only way to justify my steep learning curve is come back stronger, faster and better and go for the win, because if i dont then the car would have stayed broken in my garage for years until eventually i would end up selling it.
finding time is hard though with a 2yr old and another one due in march, theres still alot to do, but my time is free and I make everything myself so the overall costs arnt to bad.
#443
Posted 10 December 2014 - 01:33 AM
#444
Posted 10 December 2014 - 04:03 AM
you can do much when your focused, tonight ive already transferred the indicators and tomorrow ill bond in the headlight brackets. Got some material on order for my new splitter with full width diffusers, end plates and canards, the aim is to have the car complete before xmas, that way im going to be pounding around cadwell every track day i can book between january and april, only way to justify my steep learning curve is come back stronger, faster and better and go for the win, because if i dont then the car would have stayed broken in my garage for years until eventually i would end up selling it. finding time is hard though with a 2yr old and another one due in march, theres still alot to do, but my time is free and I make everything myself so the overall costs arnt to bad.

#445
Posted 11 December 2014 - 08:28 PM
Max respect fella. Doing it all yourself is a huge undertaking especially with family. Do you post on lotus forums or just here? I only ask out of curiosity.
I posted on here and seloc now, used to post on a few more forums, but getting grief for the car made me just stick to these forums.
alot of the time, if you want to see the latest pics just look for lee connor on facebook and you will find me, add me and you can see what im up to.
#446
Posted 11 December 2014 - 08:31 PM
Good luck for next season !!
#447
Posted 11 December 2014 - 09:46 PM

#448
Posted 11 December 2014 - 10:23 PM
What helps is hearing critique (mindless or not) and rising above it. You certainly showed that on here and endeared me towards your project. Others have a lot to learn on that front (myself included).getting grief for the car made me just stick to these forums.
#449
Posted 12 December 2014 - 05:33 PM
just got in from work and decided to bond in the headlight brackets, amazing how something so simple can be so messy
looks easy enough
Not when your fingers slip, going to take a week to get stikaflex off my hands now
Sat down last night and designed my front splitter with integral diffusers, the shaded green area is all diffuser, since the splitter needs to raise 35mm from the chin to the chassis, the diffuser at a conservative 8 degrees takes roughly 230mm distance so instead of creating to small diffusers like i did on my last splitter I can now create one large one, I may actually create a complete 1900mm wide one(the full width) and then build my end plates ontop them, this is looking mostly likely as im chasing the same level of front downforce as before even with a smaller surface area.
Im going to use 3mm dibond sheet to make the full splitter arrangement but once its all made ive got a big roll of carbon so im going to lay a few layers of that ontop to give it the strength it needs without being to heavy, either that im going use it as a mold to make a carbon/nomex splitter, i havent decided yet.
#450
Posted 12 December 2014 - 06:37 PM
I agree wasn't 100% on it at first but you've swayed me towards it and look forward to (hopefully) seeing it in person at some point :What helps is hearing critique (mindless or not) and rising above it. You certainly showed that on here and endeared me towards your project. Others have a lot to learn on that front (myself included).getting grief for the car made me just stick to these forums.


#451
Posted 17 December 2014 - 12:33 AM
next stage now ive fitted the indicators and lights is the front splitter.
Ive learned a few things from my previous setup, what i liked about it and what i didnt, so hopefully this will be an improvement
did a few drawings of how i wanted it to look
What im maximising this time is underbody surface area at the front so ive widened the section between the front wheels as this will allow more low pressure air an easier passage down the length of the car without wheel well interuption, these sections will also run skirts for the same reason, and will be running everything I can down to the 40mm minimum ground clearance
Then bought a sheet of 3mm dibond put the bend in it at work and fitted onto the car to check everything, tomorrow I will be fittingn my tie bars to it so i know everything fits
At the moment you can see its still to big, but i cant cut it down yet as I need to mould the carbon off it and need an overlap for resin infusion so it looks a bit crazy, but even so its still going to be 1900mm wide so im not cutting that much off it, should be interesting to see how effective it is compared to my old splitter, i might play with front diffuser angles in the wheel arches to see how steep they can run without separation.
Im still undersided on what to make my engine undertray and diffuser from as I dont want to add anymore weight to the car, currently they are made from 1mm ali and have stood the test of time, but i was thinking about 1mm carbon for the engine undertray and maybe a foam core version for the diffuser
#452
Posted 17 December 2014 - 09:06 AM
1mm carbon is too flexible for the undertray. I'd go with 2x200g cloth and a 3mm foam core. That should shave off a load of weight and be suitably rigid. Mine is 2x200g carbon and 3d core. I find this is a bit lighter than oem so you should loose more weight going for straight foam.
#453
Posted 17 December 2014 - 09:15 AM
#454
Posted 17 December 2014 - 10:14 AM
I'd considered honeycomb but I think the cost might be prohibitive
http://www.easycompo...-honeycomb.aspx
The density difference of 29kg/m3 vs 75kg/m3 is incredible but on a moulding of this size the difference isn't enough to justify the extra cost IMO. There are cheaper but these offer little benefit over pvc foam. Couple that with the need for 2 moulds if you're doing it by infusion makes it more of a ball ache. Pre-preg and an autoclave would be nice for a project like this.
#455
Posted 17 December 2014 - 12:01 PM
1mm carbon is too flexible for the undertray. I'd go with 2x200g cloth and a 3mm foam core. That should shave off a load of weight and be suitably rigid. Mine is 2x200g carbon and 3d core. I find this is a bit lighter than oem so you should loose more weight going for straight foam.
The good thing about the undertray was that it was fairly well supported in that it had 4 m8 bolts, the lip at the front, 2 m5 bolts at the rear outer edges and it also sat under the carbon sills the full length down each side, so while 1mm ali is fairly flexible, it didnt really have anywhere it could flex to hence it was ok to keep fairly light.
The one thing I didnt like about my design was was trying to get the 2 sheets of ali(undertray and diffuser) to bolt together and create a smooth transition between them, the factory puts a kink in the diffuser so they are flush when bolted together, not as easy to do myself.
What i would have liked would have been able to make to get a 1.7m long by 1.3m wide single piece that would be a undertray and diffuser combined, that way I know i will get a smooth transition.
At the moment my undertray is 1.3m wide by 1m long, if I use a 1.2x2.4m sheet I run the undertray longer, past the 14 degree bend and then run a shorter length diffuser section, this might be the way I go about it.
I have thought about using carbon with a nomex core, the problem is I use the rear subframe to jack the car up as I cant get the jack under anywhere else so im not bothered it crushing 1mm ali against the subframe as I lift it, but i would if im crushing carbon and nomex together
You could always go for a honeycomb core will be extremely lightweight, it's what we make most of our aircraft parts with
as above, on the splitter itself im going to use 2 layers of carbon each side with a 10mm nomex core which im hoping will b e stiff enough that i can get away with not having my tie bars protude outside the bodywork, effectively have them attached just behind the body, that will mean its easier to get the body on and off, the bad news is it makes it harder to quickly adjust them.
What i will also do is not run the nomex past the wheels, that way i wont have a step when the splitter ends and keeps a smoother transition as it will only be 4 layers of carbon at the last bolt points.
I'd considered honeycomb but I think the cost might be prohibitive
http://www.easycompo...-honeycomb.aspx
The density difference of 29kg/m3 vs 75kg/m3 is incredible but on a moulding of this size the difference isn't enough to justify the extra cost IMO. There are cheaper but these offer little benefit over pvc foam. Couple that with the need for 2 moulds if you're doing it by infusion makes it more of a ball ache. Pre-preg and an autoclave would be nice for a project like this.
Thats where my best mate works whos helping me with making the parts so he will sort out the materials which hes said will be the nomex(for the front splitter at least)
for the moulds we will just use the same mould for both pieces, but for the top side ill put a 10mm kink in it for when the nomex is removed.
#456
Posted 17 December 2014 - 12:54 PM
Warren will see you right with making these
#457
Posted 18 December 2014 - 08:44 PM
Makes such a difference putting the body on, I need a bigger splitter!!
#458
Posted 23 December 2014 - 09:14 PM
new rear wing turned today, need to wait till january to fit it as I need to use the bender at work to modify the the upright width.
What do you do when you have 2 dual element wings and one vehicle, hopefully over xmas I will show you
#459
Posted 23 December 2014 - 09:28 PM
I can guess.
But remember, just because you can, doesn't mean you should.
#460
Posted 31 December 2014 - 11:44 AM
similar to that, but will be alot more effective though with what im doing with it.
continued work on the carbon splitter
taped up all the holes
laid 4 layers of carbon
Just need to bag and vac it down now and send the resin through it and im 50% complete, do the same again then bond them together with nomex
1 user(s) are reading this topic
0 members, 1 guests, 0 anonymous users