I could do that not a big job to remove the s/c with the access port now, just have to remove the pax seat and rear shelf. It may be possible to loop the cooling fluid from the manifold through the new cooler cores as a temp measure?I wouldn't say no to Lees idea if it works. Would be nice to try it on the Dutch software with before and after graphs.
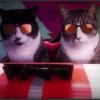
Supercharged Intake Temps
#321
Posted 27 June 2014 - 06:54 AM
#322
Posted 27 June 2014 - 07:23 AM
#323
Posted 27 June 2014 - 10:32 AM
If you're going to all of that grief, you might just as well do it properly and bin the LSJ inlet manifold. Mount the SC the other way up at the bottom of the engine where the aircon compressor would normally be, make an adapter plate to take the charge air and fire it into the rest of the ProAlloy turbo's charge cooler and out of that and back into the engine through the Saab's cast manifold (sorry, still don't trust the plastic manifolds to hold boost). Would mean a lot more post-charger volume, so boost and compression induced temps would drop even before the charge cooler gets to work. Winstar asked a question about how much we'd be prepared to pay for a totally new manifold design and we collectively went remarkably quiet when it was obvious that it was going to cost more than £50 to design and produce.
That's the way to go Matt, that would be the best solution, I actually have a Saab manifold here will dig it out and have a look, so here is the manifold so we need to invert the s/c and have some other attachment from the charger into a turbo charge cooler.
Edited by NickB777, 27 June 2014 - 10:46 AM.
#324
Posted 27 June 2014 - 10:45 AM
that would be the best solution
Still not sure it's best as it raises further questions like "if I'm going to that level of hassle, would a centrifugal charger make more sense; it certainly would from a packaging point of view?". Then the inevitable, "if I'm using the Saab inlet, why not use the Saab exhaust manifold and fit a bloody turdo instead?". Which of course then brings you to the "don't build what you can already buy" truism.
#325
Posted 27 June 2014 - 10:48 AM
ok should have said that may be a solution, looking at the exige s/c setup with the charge cooler on top of the engine they may use a manifold similar to the saab one
I personally prefer a s/c setup to turbo one if there is a sensible way of doing this great that also goes for sensible cost
Edited by NickB777, 27 June 2014 - 10:49 AM.
#326
Posted 27 June 2014 - 10:49 AM
#327
Posted 27 June 2014 - 10:50 AM
how about a try with one if it was to work you could always try 3d printing?
looking at the lotus manifold it is a lovely bit of kit
Edited by NickB777, 27 June 2014 - 11:01 AM.
#328
Posted 27 June 2014 - 11:09 AM
Ohhh thats pretty, and gives flexibility of cooling etc..
Now, I know its somewhat overpriced, but you could get a webCON DCOE inlet manifold (or have one made up for less), add some jenveys or simple tubes as the butterfly isnt needed, then add the Jenvey plenum and you are 75% there... if you assume that its a mere 25% to fit the SC lower down etc
#329
Posted 27 June 2014 - 11:30 AM
I'd say I could do it cheaper than the numbers Scuffers quoted but only because I can do all the CAD, flow/structural calculation and analysis having done it for a living in the past (and could probably get some of my grads to chip in on it) But yes the price people where willing to pay (considerably less than PA charge for the turbo setup that is nothing more than a mulit-pass core with some plenums welded on) and the size of the market means it not worth the effort.If you're going to all of that grief, you might just as well do it properly and bin the LSJ inlet manifold. Mount the SC the other way up at the bottom of the engine where the aircon compressor would normally be, make an adapter plate to take the charge air and fire it into the rest of the ProAlloy turbo's charge cooler and out of that and back into the engine through the Saab's cast manifold (sorry, still don't trust the plastic manifolds to hold boost). Would mean a lot more post-charger volume, so boost and compression induced temps would drop even before the charge cooler gets to work. Winstar asked a question about how much we'd be prepared to pay for a totally new manifold design and we collectively went remarkably quiet when it was obvious that it was going to cost more than £50 to design and produce.
#330
Posted 27 June 2014 - 11:35 AM
in reality 3D printing has some pretty big limitations in Laser sintered metal in terms of what you can print due to overhangs and warpage from the residual stresses not least there is only one machine that can do anything like the size required, IIRC the only one is owned by Daimler to print prototype engine blocks. It's only real use for anything large or with high temps/stress is to make a prototype to create a casting mould or moulds for compositeshow about a try with one if it was to work you could always try 3d printing? looking at the lotus manifold it is a lovely bit of kit
Edited by Winstar, 27 June 2014 - 11:37 AM.
#331
Posted 27 June 2014 - 12:05 PM
I know people laugh at the stuff but the simplest way to impliment a different design is:
1. Dbilas inlet manifold
2. Pro alloy exchanger.
#332
Posted 27 June 2014 - 12:05 PM
They are very effective but nowhere near as effective as a air con system. Laminovas is also a restriction. As the air can't pass through them quick enough the pressure before them is building up causing more heat
sorry, bit late to this one!
AC is a non-starter, just think about the heat capacity your trying to 'move'
even big AC installs (on cars) are usually less than 10Kw, you need something around 2-3 times that for this job
I'd say I could do it cheaper than the numbers Scuffers quoted but only because I can do all the CAD, flow/structural calculation and analysis having done it for a living in the past (and could probably get some of my grads to chip in on it) But yes the price people where willing to pay (considerably less than PA charge for the turbo setup that is nothing more than a mulit-pass core with some plenums welded on) and the size of the market means it not worth the effort.If you're going to all of that grief, you might just as well do it properly and bin the LSJ inlet manifold. Mount the SC the other way up at the bottom of the engine where the aircon compressor would normally be, make an adapter plate to take the charge air and fire it into the rest of the ProAlloy turbo's charge cooler and out of that and back into the engine through the Saab's cast manifold (sorry, still don't trust the plastic manifolds to hold boost). Would mean a lot more post-charger volume, so boost and compression induced temps would drop even before the charge cooler gets to work. Winstar asked a question about how much we'd be prepared to pay for a totally new manifold design and we collectively went remarkably quiet when it was obvious that it was going to cost more than £50 to design and produce.
if you have the resources, go for it... more than happy to help out with this...
the Lotus one posted up is OK, but has issues, you have to remember that the more air volume between the throttle and the engine the more problematic in terms of throttle response, as well as idle/low flow rate instability.
Also, air to air just does not work in a mid engined setup without some major compromises.
somebody mentioned the restrictive nature of the laminovas, and yes, at higher (air) flows that's a significant problem, with the original M62 install probably not so bad, but with 300+hp airflows they will be significant (more restriction = more parasitics and more heat).
ultimately, water is the way forward, using as high a density core as possible without causing significant air restriction, hence why I had the sandwich coolers made for the Honda's (that Lee is now using).
the real issue here is as usual, you get space limited.
re: exhausts, yes, the more restrictive, the more MAP pressure you will get, more MAP = more heat & parasitics.
#333
Posted 27 June 2014 - 12:39 PM
They are very effective but nowhere near as effective as a air con system. Laminovas is also a restriction. As the air can't pass through them quick enough the pressure before them is building up causing more heat
sorry, bit late to this one!
AC is a non-starter, just think about the heat capacity your trying to 'move'
even big AC installs (on cars) are usually less than 10Kw, you need something around 2-3 times that for this job
I'd say I could do it cheaper than the numbers Scuffers quoted but only because I can do all the CAD, flow/structural calculation and analysis having done it for a living in the past (and could probably get some of my grads to chip in on it) But yes the price people where willing to pay (considerably less than PA charge for the turbo setup that is nothing more than a mulit-pass core with some plenums welded on) and the size of the market means it not worth the effort.If you're going to all of that grief, you might just as well do it properly and bin the LSJ inlet manifold. Mount the SC the other way up at the bottom of the engine where the aircon compressor would normally be, make an adapter plate to take the charge air and fire it into the rest of the ProAlloy turbo's charge cooler and out of that and back into the engine through the Saab's cast manifold (sorry, still don't trust the plastic manifolds to hold boost). Would mean a lot more post-charger volume, so boost and compression induced temps would drop even before the charge cooler gets to work. Winstar asked a question about how much we'd be prepared to pay for a totally new manifold design and we collectively went remarkably quiet when it was obvious that it was going to cost more than £50 to design and produce.
if you have the resources, go for it... more than happy to help out with this...
the Lotus one posted up is OK, but has issues, you have to remember that the more air volume between the throttle and the engine the more problematic in terms of throttle response, as well as idle/low flow rate instability.
Also, air to air just does not work in a mid engined setup without some major compromises.
somebody mentioned the restrictive nature of the laminovas, and yes, at higher (air) flows that's a significant problem, with the original M62 install probably not so bad, but with 300+hp airflows they will be significant (more restriction = more parasitics and more heat).
ultimately, water is the way forward, using as high a density core as possible without causing significant air restriction, hence why I had the sandwich coolers made for the Honda's (that Lee is now using).
the real issue here is as usual, you get space limited.
re: exhausts, yes, the more restrictive, the more MAP pressure you will get, more MAP = more heat & parasitics.
Don't completely agree with the aircon statement. You need about 0.25 KW to cool the charge 1 degree. That's at about 6,500 rpm and 1 bar boost (about 250 grams of air per second). With 10KW you can theoretically cool it by 40 degrees. The good thing about airco's however is the efficiency, which is far above 100%. To get 10KW cooling power, you need a lot less from the engine. I do agree that it doesn't seem the right way to go in this case.
Instead of doing it the right way and re-engineering/designing a lot of expensive parts, what's wrong with water injection? I know I'm slow, but can someone please spell it out for me. Looks like in similar situations people kind of like it and it doesn't require any big changes. Plus you don't need to use it. Lets face it, on public roads, you don't need the extra charge cooling. On track you do. So on track you use water injection and a special map for that. It won't last for hours, unless you get a real big tank, but most people will only do stints of about half an hour or less. Not the best of solutions, but to me it looks a lot more simple than designing a new manifold/cooling system.
#334
Posted 27 June 2014 - 12:58 PM
Don't completely agree with the aircon statement. You need about 0.25 KW to cool the charge 1 degree. That's at about 6,500 rpm and 1 bar boost (about 250 grams of air per second). With 10KW you can theoretically cool it by 40 degrees. The good thing about airco's however is the efficiency, which is far above 100%. To get 10KW cooling power, you need a lot less from the engine. I do agree that it doesn't seem the right way to go in this case.
Instead of doing it the right way and re-engineering/designing a lot of expensive parts, what's wrong with water injection? I know I'm slow, but can someone please spell it out for me. Looks like in similar situations people kind of like it and it doesn't require any big changes. Plus you don't need to use it. Lets face it, on public roads, you don't need the extra charge cooling. On track you do. So on track you use water injection and a special map for that. It won't last for hours, unless you get a real big tank, but most people will only do stints of about half an hour or less. Not the best of solutions, but to me it looks a lot more simple than designing a new manifold/cooling system.
??
without knowing the air-flow (or more specifically, air mass/second) that's just a random number?
to put some numbers to this, to cool 13,000liters/min (at atmospheric pressure and temp - this is ~240G) from 85C to 60C needs ~10Kw of cooling
13,000L/min is only ~250Hp's worth of air...and that's only a 25C reduction in temps....
#335
Posted 27 June 2014 - 01:19 PM
Just to completely derail this thread with a useless contribution, take the M62 off, and fit a twin-scroll K04 that comes standard on US LNF engine (and the Astra J VXR / Insignia in the UK). Fit a secondary chargecooler matrix and you'll have no more IAT issues... This all all "bolt-on" if using a B207 / Z20NET.
#336
Posted 27 June 2014 - 02:25 PM
That frankenstein only fit's in Lee's car
#337
Posted 27 June 2014 - 02:28 PM
Just skimming through the last postings, but before this derails into imaginary manifolds + relocated SC's (I would love to build that), did anybody check the available space we have to work with?? Our cast oil filter causes a massive obstruction for such solution and I don't think many are willing to relocate it (=> sawing it off and welding some oil hose bungs onto your block.) so they can fit a better manifold...
#338
Posted 27 June 2014 - 02:44 PM

#339
Posted 27 June 2014 - 02:50 PM
Don't completely agree with the aircon statement. You need about 0.25 KW to cool the charge 1 degree. That's at about 6,500 rpm and 1 bar boost (about 250 grams of air per second). With 10KW you can theoretically cool it by 40 degrees. The good thing about airco's however is the efficiency, which is far above 100%. To get 10KW cooling power, you need a lot less from the engine. I do agree that it doesn't seem the right way to go in this case.
Instead of doing it the right way and re-engineering/designing a lot of expensive parts, what's wrong with water injection? I know I'm slow, but can someone please spell it out for me. Looks like in similar situations people kind of like it and it doesn't require any big changes. Plus you don't need to use it. Lets face it, on public roads, you don't need the extra charge cooling. On track you do. So on track you use water injection and a special map for that. It won't last for hours, unless you get a real big tank, but most people will only do stints of about half an hour or less. Not the best of solutions, but to me it looks a lot more simple than designing a new manifold/cooling system.
??
without knowing the air-flow (or more specifically, air mass/second) that's just a random number?
to put some numbers to this, to cool 13,000liters/min (at atmospheric pressure and temp - this is ~240G) from 85C to 60C needs ~10Kw of cooling
13,000L/min is only ~250Hp's worth of air...and that's only a 25C reduction in temps....
Not quite a random number, I mentioned 250 grams/sec. Specific heat of air at the temperatures we're talking about is about 1KJ per kg per degree. So 0.25 KJ per kg per degree per second, or 0.25KW per kg per degree. But that's theory and not taking any efficiencies into account.
What about water injection as a quick and dirty solution?
#340
Posted 27 June 2014 - 02:52 PM
1 user(s) are reading this topic
0 members, 1 guests, 0 anonymous users