
Project Fracas - 6Sp A20Nft
#1041
Posted 08 September 2018 - 09:59 AM
#1042
Posted 08 September 2018 - 06:56 PM
had 5 mins (after embracing my inner bogan)
Not sure how many will understand that

Put Holden across the back, will fill out that fat arse nicely
Don't forget to put HSV somewhere on it as well
#1043
Posted 09 September 2018 - 08:23 AM

i didn't want to stick a lotus badge on it, and thought the GMC badge fit the space well. A further consideration was that it'll still be registered as an Opel, and not being the most ordinary looking nor unremarkable car, i can imagine it'll have its plate run by the cops (at least more often than normal) ... i don't want to invite being pulled over because the registration system says Opel, and the badge says Lotus. just trying to avoid problems
#1044
Posted 13 September 2018 - 08:34 AM
im going to try my hand at structural carbon composites to reinforce the rear clam across the bumper and reinforce the rear arch location, as well as mounting to the rear chassis... i have 245gsm twill end-of-roll CF and some 2k epoxy resin sitting idle. i did some reading on the bonding of such a strong and rigid composite tube to something more soft and elastic like the polyester chopped mat body, and ultimately it seems the best thing is to sikaflex it together. ive previously used 255FC for other structural body components, and i think that would be the way to go again now. funny how it gets little notice in discussion of strong single part polyurethane adhesives. 292 is my usual go-to high strength adhesive, and 221 my 'do everything' adhesive...
255 - tensile: 870psi, lap/sheer: 580psi, elongation: ~400%
292 - tensile: 550psi, lap sheer: 360psi, elongation: >300%
221 - tensile: 260psi, elongation: > 500%
so, making the tube... i had the idea of thermo-forming some PVC tube. thats feasible to do in position on the car with a hotair gun. splice in some T fittings and send some tubes forward in the direction of the chassis mounts (as post above). ill transition those PVC tubes to alloy, and use a surface abrasion on the alloy to eventually bond the aluminium stalks direct to the epoxy.
so ive got that 245gsm twill. ill cut it into 10cm strips, run one length of twill longitudinally down the PVC , then wrap 2 further up and down in crossing 90deg laminates. so three layers at 45deg orientations. tie over the T junctions, wrap the aluminium. then use plain old packing tape to compress the wrap's form to the tube and get good impregnation (apparently it releases ok from epoxy).
so, to mounting it, i had a moment of clarity, and came up with this... 2 longitudinal tubes coming forward from the clam, and picking up the wing/body uprights. ill use some aluminium hydraulic tube clamps, and that will let me adjust things in position, and button it all up.
need to tidy up the files a bit, and its off to the laser cutter guy
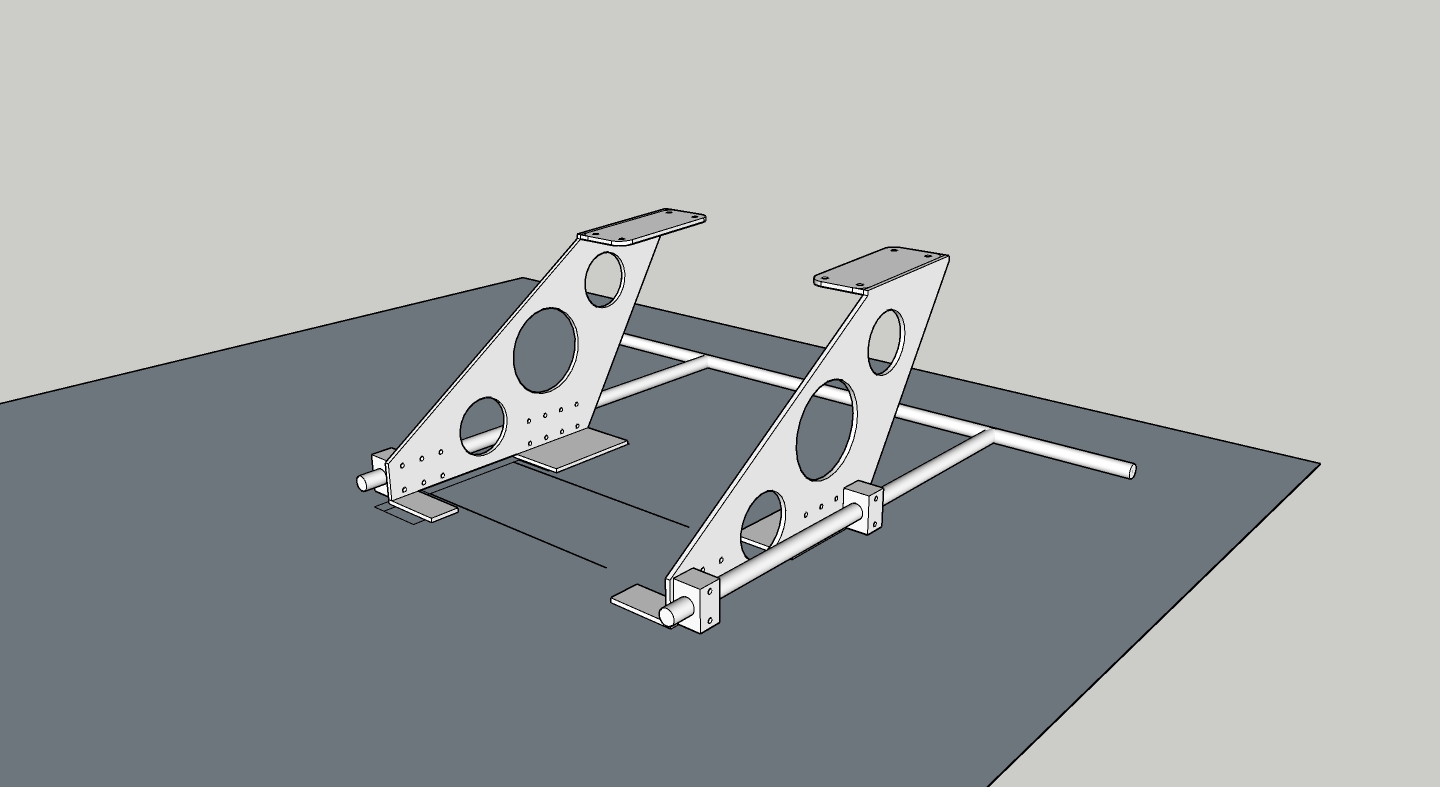
#1045
Posted 22 September 2018 - 12:27 PM
Edited by Doctor Ed, 22 September 2018 - 12:27 PM.
#1046
Posted 22 September 2018 - 01:17 PM
Edited by Doctor Ed, 22 September 2018 - 01:17 PM.
#1047
Posted 22 September 2018 - 03:05 PM
#1048
Posted 24 September 2018 - 03:39 PM
Absolutely nothing a bit of filler and a surform can’t make perfect. Flowcoat over the top

#1049
Posted 24 September 2018 - 04:33 PM
Whats the green coloured filler - epoxy resin?
#1050
Posted 24 September 2018 - 06:04 PM
its just polyester resin that's not 100% cured yet (green phase cure)
Edited by Doctor Ed, 24 September 2018 - 06:08 PM.
#1051
Posted 25 September 2018 - 07:47 AM
Bet that took a while to complete.
#1052
Posted 25 September 2018 - 10:11 AM
yep, fast is not how i would describe it
#1053
Posted 25 September 2018 - 09:14 PM
tried something new today... i needed to cut out reprofile 2 big ass holes on each side left over from the dry-break fuel system mounts. again a compound convex curve. so got some relatively thick (~5mm) thermoplastic sheet and the heatgun out. got the basic form of the thermoplastic made based on the section of body immediately next to the hole, then did some minor 'in position' forming to get the contour a little better fitted (tricky as when soft it was easy to let the plastic form into the hole rather than ride flush over it). used hot glue to then seal and hold the thermoplastic form to the surface (releases cleanly and easily from the existing gelcoat).

Edited by Doctor Ed, 25 September 2018 - 09:14 PM.
#1054
Posted 26 September 2018 - 10:35 AM
125mm rubber velcro sanding plate on the grinder. pack of 60grit discs, windy day (fcuk you neighbours!) and off we go. ive never sanded fibreglass like this before, and jesus, its amazing. the control is brilliant, the rate of material removal is predictable and very finely adjustable with hand/disc position. and whilst i was initially a bit held back running the disc dead flat on the panel surface (normally a big no-no for me with an angle grinder) holy sh*t *sun ray pieces through the clouds, illuminating me with enlightenment* once the focussed material removal is done with the disc angled into the workpiece, laying it dead flat on the panel surface and moving it in circles like a buffing machine is next level! the rate of removal slows, and it blends complex contours like a fcuking boss. it doesn't flatten anything at all, it rolls the highs and lows and almost instinctively take out unwanted high spots whilst maintaining the curve and profile of the piece in general. such a pleasure to work with.
#1055
Posted 26 September 2018 - 11:08 AM
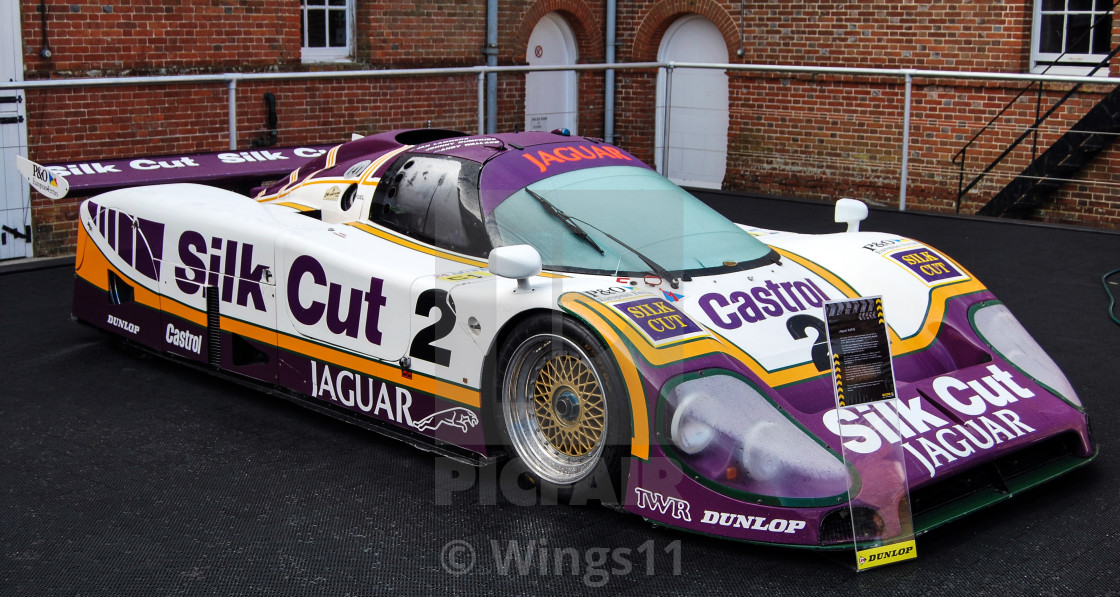
#1056
Posted 27 September 2018 - 08:04 AM
ideas on the wing support structure.
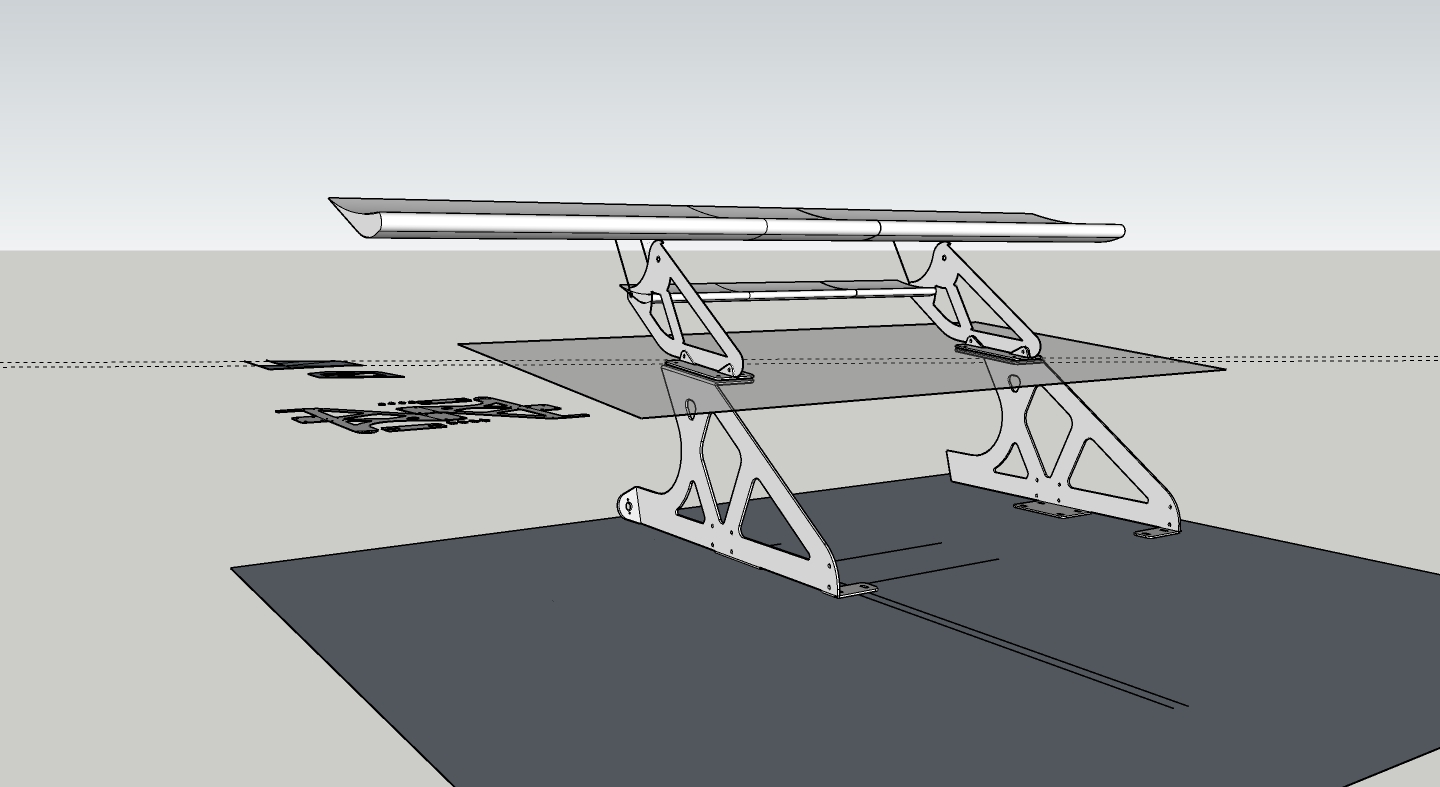
#1057
Posted 27 September 2018 - 02:52 PM
Ideal use of garden furniture
#1058
Posted 27 September 2018 - 10:38 PM
#1059
Posted 28 September 2018 - 04:10 AM
...Plastic fantastic!
#1060
Posted 28 September 2018 - 05:54 AM
1 user(s) are reading this topic
0 members, 1 guests, 0 anonymous users