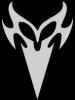
Track User - Warning I
#21
Posted 09 March 2005 - 02:28 PM
#22
Posted 09 March 2005 - 03:51 PM
Increasing the bolt size to M12 IS an alternative - BUT not one I would recommend, nor should it be necessary.Is it worth considering taking the bolts up a size? It would mean drilling out the old thread and tapping to a bigger size, but if there is plenty of "meat" there, then a larger diameter bolt would be a good move.
Steve
Two "bad" things happen, when you increase the bolt diameter:
1/ You make the bolt stiffer compared to the clamped material. This is a bad thing when it comes to loads trying to separate the clamped parts, because the screw feels more of the external load (but it makes no difference when it comes to shear loads).
2/ You decrease the relative distance from the bolt (hole) center compared to the bolts diameter. Good, common practice when designing preloaded bolt joints is to make sure, that the distance to the edges measured from the center of the bolt is at least 1½ to 2 times the bolt diameter (which might not even be the case with the original parts).
HOWEVER, these 2 points are certainly not a big problem when changing from M10 to M12, so in this case they are more theoretical observations.
Of course the obvious good thing and the primary reason for increasing the bolt size is the potentially higher clamp load. I think (though, not having done any calculations

So, 10.9 bolts (with higher torque and perfectly clean clamped mating surfaces) would IMO be the better solution

Anyway, seems like that cured the problem for Ricky.

#23
Posted 09 March 2005 - 04:09 PM
Good idea, I was thinking about that tooProper torque is of course the first and most important thing, but Lotus also prescribes a threadlocker for these bolts: Permabond A130
You can replace this with Loctite 243, which is pretty similar if you can't get Permabond.
Even though this has no influence on the actual clamping force (might provide some thread lubrication while installing, but not much), it does increase the vibration resistance after it has cured and reduces the risk of the bolts 'un-screwing'.
This is a medium strength threadlock, so it will still release OK with a little force.
It's just 1 of the factors to consider.. Use good bolts (and replace often.. cheap insurance), torque properly and use the right procedures (as described brilliantly above), use the required threadlock compound.
Then this problem should not happen at all.
Anyone who uses a car on track (any car, not just an Elise or VX..) should do regular 'spanner checks' on suspension bolts. Things get loose, bent or otherwise over-stressed.
Bye, Arno

Usually "vibration loosening" only happens when there is insufficient clamping force and/or friction ie. when the clamped parts can move relative to each other. So if you make sure, that does not happen (as Arno underlines the importance of), then the threadlocker does not have to do what it is meant to do (ie. stop loosening). However, it cannot hurt to use it - and better safe than sorry!!.
Threadlockers also provide good corrosion protection, so the bolts will proably be easier to unscrew then very rusty ones.
#24
Posted 09 March 2005 - 05:43 PM
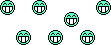

#25
Posted 09 March 2005 - 06:21 PM

#26
Posted 09 March 2005 - 06:59 PM
#27
Posted 09 March 2005 - 07:56 PM
Ok i'll change it!!Indeed, the damper is in the way of one bolt... Just undo the damper from the top and push it on the side, no pb at all...
#28
Posted 10 March 2005 - 10:35 AM
#29
Posted 10 March 2005 - 03:34 PM
Well, it could pose a problem... but probably won'tJust replaced this screws,i used 12.9 grade with loctite 243 and torqued to 70Nm with no problem!!
![]()
On rear however i changed only 1 screw because i don't wanted to pull down the damper to replace the other screw,doing this could be a problem??

If you replace only one of the two bolts, tighten the new bolt to 70 Nm (25 Nm more than the old bolt)
and the two bolts are closely spaced, you will to some extent relieve the pretension in the old bolt, that is still installed. So, I would strongly recommend, that you check the other bolt and make sure it is still tight ie. tighten to 45 Nm (but then if you can check this, then I would assume that you could just as well replace the bolt).
This is pretty much the same reason, you tighten bolts in two stages and each time in a certain order (or pattern) when assembling large groups of bolts, for instance wheels or cylinder heads (cylinder head bolts have two different tightening torque values - the first stage torque value is usually around 50-70% of the second/final torque value), so that you get an evenly distributed clamp load (same pretension in all bolts).
Of course, it would better to use bolts tightened to the same torque (but they don't have to be the same strength grade - you can use one 10.9 and one 12.9 bolt, both tightened to 60 Nm).
Edited by Saber, 10 March 2005 - 03:34 PM.
#30
Posted 10 March 2005 - 03:38 PM
I'm located in Fredericia - in the middle of Esbjerg and Copenhagen (actually next to the Lillebelt Bridge)Saber, where are you located ?
I'm a regular visitor to Copenhagen/Esberg.. all work related.

#31
Posted 10 March 2005 - 03:42 PM
Yes, they willQuestion
Will m10 x48(not 50) be ok 10.9
Lotusparts.com hold these now

Only 1½ thread is "missing", so as long as you don't strip the threads when tightening the 10.9 bolts, everything will be okay !
#32
Posted 10 March 2005 - 03:55 PM
#33
Posted 10 March 2005 - 04:07 PM

Edited by Saber, 10 March 2005 - 04:11 PM.
#34
Posted 10 March 2005 - 04:17 PM
#35
Posted 10 March 2005 - 05:39 PM
Okay, you are also talking about the wheel spacers....wheel spacer on back 5mm each side. Shims standard.

Well, basically the same story as with the hub carrier bolts - though, the wheel bolts are probably M12...
However, (most) wheel bolts are not tightened to the yielding point, as they are often removed (and not replaced when reassembling). When using a 5 mm wheel spacer, around 3 threads less are engaged, so just make sure you don't strip threads when tightening to specified torque (usually around 90-100 Nm for M12 wheel bolts), but I think it would take some serious "over-torqueing" to do that, well, depending on the number of threads engaged

To be safe, you can get some longer bolts for use with spacers (especially thicker spacers, sometimes they come with the spacers), which might be a good idea when going to track days.
The shim (hub carrier) only being one (?) mm thick does not make much of difference to the number of threads engaged.
Edited by Saber, 10 March 2005 - 05:41 PM.
#36
Posted 11 March 2005 - 05:48 PM
I'm located in Fredericia - in the middle of Esbjerg and Copenhagen (actually next to the Lillebelt Bridge)Saber, where are you located ?
I'm a regular visitor to Copenhagen/Esberg.. all work related.
Know Fredericia railway station well

Occasionally have a few days playing 'tourist' in either Copenhagen or Esberg. PM me your e-mail address and perhaps we could meet up for some


Dave K
#37
Posted 12 March 2005 - 08:00 AM
I have 10mm spacers at the front, and got longer M12bolts accordingly.To be safe, you can get some longer bolts for use with spacers (especially thicker spacers, sometimes they come with the spacers), which might be a good idea when going to track days.
I was told by a mech engineer that a bolt needs to screw into the hub

#38
Posted 15 March 2005 - 02:19 PM
6 threads - sounds about rightI have 10mm spacers at the front, and got longer M12bolts accordingly.
To be safe, you can get some longer bolts for use with spacers (especially thicker spacers, sometimes they come with the spacers), which might be a good idea when going to track days.
I was told by a mech engineer that a bolt needs to screw into the hubfor at least SIX threads to offer maximum holding strength.


Generally speaking only a few threads actually carry the (pre-)load (because of the thread geometry), so very often the threads of the two parts, screw and "nut" (hub), will excert some local yielding in order to distribute the load on enough threads to carry the load without thread stripping. Therefore, in this regard brittle materials are unfit.
3 to 6 threads, depending on the hub material strength, are probably enough to carry the load if you do the (engineering) math. 6 or 7 threads equals the height of the type of nut, you would typically use for a preloaded bolt joint, that is: nut height = 0.8 to 1 x D(screw diameter)
But such a nut is made out of a material with slightly higher (proof) strength (e.g. strength grade 10, for 10.9 screws) than the screw, whereas the material of the hub probably (

Therefore, at least the screw diameter, i.e. 12 mm should be screwed in (= 7 threads, anyone higher ?

But that's just me being meticulous...


6 will probably be enough too

To be safe, and like Ricky simply replace the standard bolts with some that are 5 or 10 mm (=thickness of spacer) longer.
#39
Posted 15 March 2005 - 02:30 PM
sounds like a good idea - you bring the bolts and torque wrench and I'll bring theKnow Fredericia railway station well
Often have to change there when I can't get a through train from Copenhagen to Esbjerg.
Occasionally have a few days playing 'tourist' in either Copenhagen or Esberg. PM me your e-mail address and perhaps we could meet up for someand torque 'bolts'
![]()
Dave K


Have PM'd you...
#40
Posted 16 March 2005 - 05:59 PM
1 user(s) are reading this topic
0 members, 1 guests, 0 anonymous users