

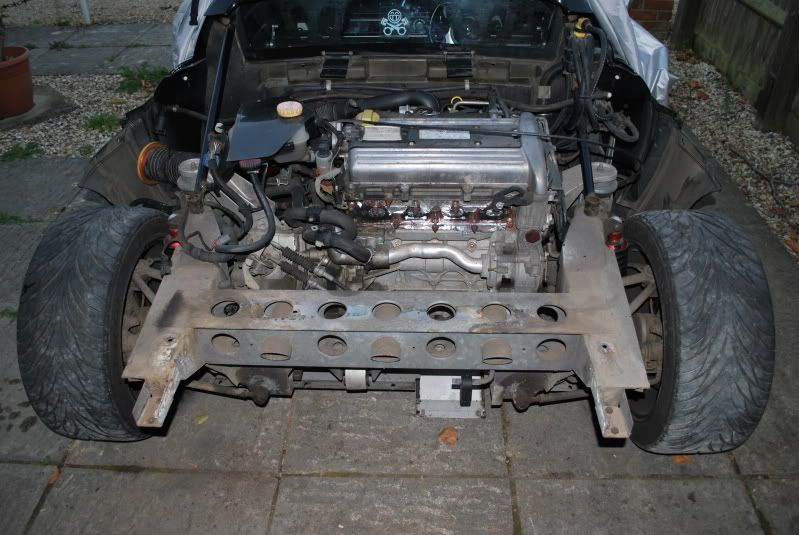
Also dremelled out the failed clam to boot fixings, to be replaced with stainless rivnuts

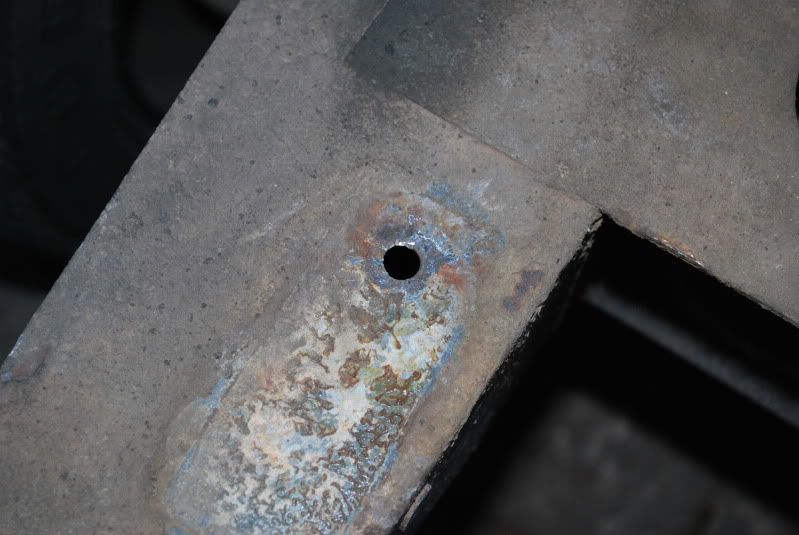
The manifold crack all but dissapeared after I'd slackened off the studs

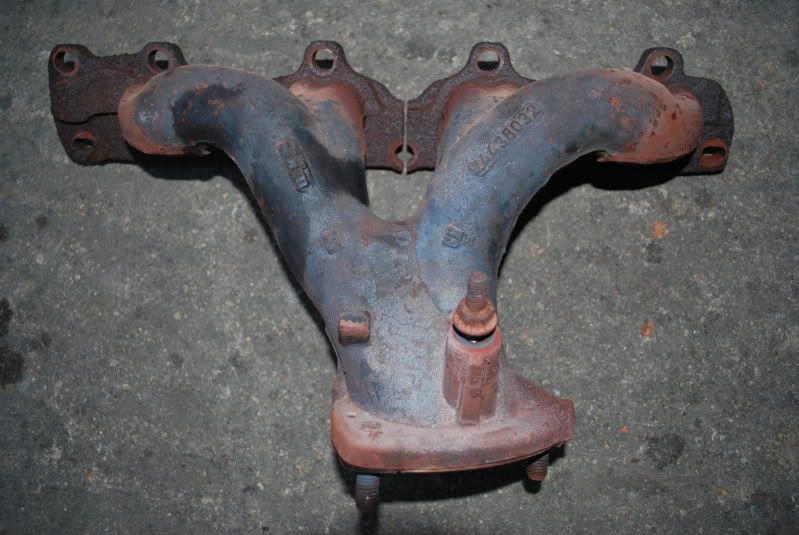
I'll give everything a good clean tomorrow I think

Posted 26 September 2009 - 09:08 PM
Posted 26 September 2009 - 09:31 PM
Posted 26 September 2009 - 09:40 PM
Not reallyadam, is there anything in the corner, behind drivers seat that can rattle alot? Got a bitch of a rattle, comes on about 3k rpm. Very tinny, doesnt sound like it comes from engine bay...
Posted 27 September 2009 - 03:22 AM
Posted 27 September 2009 - 08:42 PM
Posted 27 September 2009 - 08:45 PM
Posted 29 September 2009 - 12:50 PM
Posted 29 September 2009 - 12:53 PM
Posted 29 September 2009 - 12:56 PM
seat, belts, nope - nothing ever been removed
TBH, i was hoping to get some ideas before i spend a few hours removing it all and end up with 2 rattles
Posted 29 September 2009 - 04:25 PM
seat, belts, nope - nothing ever been removed
TBH, i was hoping to get some ideas before i spend a few hours removing it all and end up with 2 rattles
Paul your seatbelt bolts are loosecertainly the pax one is
![]()
DG
Posted 29 September 2009 - 06:24 PM
Around 4 hourscome on then how long did it take to get the rear clam off?!
Posted 04 October 2009 - 06:30 PM
Posted 04 October 2009 - 06:44 PM
Posted 04 October 2009 - 06:52 PM
Posted 04 October 2009 - 06:57 PM
Posted 04 October 2009 - 06:57 PM
Posted 04 October 2009 - 06:58 PM
This is classed as maintenancelooks good mate and you making progress now , will there be a time when your car is finished lol
Posted 04 October 2009 - 07:05 PM
This is classed as maintenancelooks good mate and you making progress now , will there be a time when your car is finished lol
Posted 04 October 2009 - 07:05 PM
Posted 04 October 2009 - 07:06 PM
Dohyou should have measured the distance between the disc face and chassis
![]()
I used a steel ruler and a tape measure, there is a lip at the bottom of the chassis (where the subframe bolts to the chassis) the distance between that lowest lip and the outer face of the disc was 176mm on mine
0 members, 1 guests, 0 anonymous users