
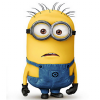
Big Power Vxt Project
#221
Posted 01 February 2011 - 10:12 PM

#222
Posted 02 February 2011 - 05:30 AM

#223
Posted 02 February 2011 - 11:07 AM
'chris', on 02 Feb 2011 - 05:30 AM, said:
And they produce more than 400 hp (with a satisfactory reliability) ?
Why GM don't "copy" b207 and z20net design on the Z20LEH ?
Erm chris,
GM most powerful 4 pot is indeed based on the B207/z20ne* family, remember the 265hp engine in the Opel GT ? In the US it also has a GM certified remap at 304hp with full warranty, with no change in the engine at all.
#224
Posted 02 February 2011 - 01:15 PM
'chris', on 01 Feb 2011 - 3:59 PM, said:
I am wondering how you can efficiently spray oil in a such restricted windows (when the piston is on BTC) with jets which have been designed for a BMW with another oil circuit and a different engine design.
Moreover your oil spray is strongly disymetric on the bottom of the piston with this design of jet installed on crankshaft bearings.
Compared with with the OEM Z20LET drilled conrods,I am pretty sure that the general efficiency result is worst with this system.
The BMW jets function correctly, I tried many other types, VW, Renault, Ford Fiat etc and with the correct angle they do an excellet job of cooling the underside of the piston.
The small hole in the con rod is there to lubricate the cylinder bores not cool the underside of the piston, but there is enough oil spray from the jet to lubricate the cylinder walls.
Also there is no noticable drop in oil pressure.
The oil jet fitment has been tried and tested on the earlyier C20LET as well as the ZLET, both types of engines makeing over 500BHP (600BHP in two cases)
Steve
#225
Posted 02 February 2011 - 05:13 PM
'chris', on 02 Feb 2011 - 05:30 AM, said:
And they produce more than 400 hp (with a satisfactory reliability) ?
Why GM don't "copy" b207 and z20net design on the Z20LEH ?
I've not seen the con rod ones but the oil pressure will never be high enough to over come the acceleration on the up stroke of the piston so you will only get cooling flow on the down stroke, but you don;t need it to constantly flowing as the heat transfer properties of oil are so much higher than air. In fact there is an argument that you don't even need them as you don't need to meet the EuroIV emissions so can map the engine cooler.
The reason they aren't on the LEH is because the base engine achitecture is over 20 years old so from a time when combustion temps where lower. The other reason is that the LEH upgrade was done on a budget GM where most pissed off that they couldn't just stick a bigger turbo on and remap it.
#227
Posted 03 February 2011 - 02:36 PM
'Nev', on 03 Feb 2011 - 2:13 PM, said:
Just ordered another 350 quids worth of stuff and written up some more blurb on theblog about MAFs, air tracts etc.
Things are progressing, slowly but surely.
#
# The inlet air pipe that feeds (roughly) atmospheric air to the turbo compressor housing (i.e. unboosted air).
this actually vents the boosted air back to the inlet , depending on the AMAL valve duty cycle. Its all metered air so the ecu expects to see it.
I would also advise to heat shield the actuator as they aren't totally heat proof and can melt, causing them to run uncontrolled boost (which is scarily fun)
#228
Posted 03 February 2011 - 03:36 PM



#229
Posted 03 February 2011 - 03:50 PM

#230
Posted 03 February 2011 - 07:59 PM
#231
Posted 03 February 2011 - 10:04 PM
Edited by Nev, 03 February 2011 - 10:07 PM.
#232
Posted 05 February 2011 - 08:38 PM
#233
Posted 06 February 2011 - 11:40 AM
'Nev', on 03 Feb 2011 - 10:04 PM, said:
Duncan, I'm still in a quandry over what size of inlet track to make. I am currently waiting on 2 sources for info on MAFs, it's bloody hard to get calibration curves and physical sizes out of them as they simply aren;t used to individuals asking such detailed questions. Thankfully, I have already got the exact spec for Bosch 92mm MAF with calibration curve, but it can only flow 1.2 Tons/Hour before the 5v signal will max out. If I tune to 500 BHP then I calculate that I will need approx 1.55 Tons of air/hour - hence I need something in the region of a 100mm MAF. This is concurs by the big american V8s such as the 500 BHP LS7 - that uses a 102mm MAF.
If I can't find a larger MAF for sensible money I will take the old sensor out of my 70mm MAF and fit it into my own alu tube and the mapper can mathematically scale up the calibration curve from the OEM 60mm venturi to the new I/D of my alu pipe. However, this wont be super accurate probably.
The crank breather hose was wrapped in heat tape today. I was going to make an alu heat shield, but the sapce was too tight, so far easier to wrap it.
The airbox is also concerning me, it was only designed to flow for 200 BHP, the relatively small filter surface area will undoubtably cause a pressure loss. I am scared of starting yet another mini project and designing/building a new one with a huge filter off some V8.
Appologies Nev you PM'ed me about this before Xmas but I was snowed under as work and i forgot.
in terms of pressure loss due to the diameter then a 1m smooth stright pipe will have the folloing
D[mm]......V[m/s].......dP[Pa]
57.........135.79.......3147.3
70.........90.04........1077.5
80.........68.93........537.1
92.........52.12........259.2
102........42.40........151.4
as for post turbo it still needs to be bigger than a ratio of the inlet and outlet pressure as the temp will be alot higher and therefore not an exact change in density (if you really want to calculate it you need to non-dimensionalise the air flow using m*sqrt(t/p)clicky
Edited by Winstar, 06 February 2011 - 11:43 AM.
#234
Posted 06 February 2011 - 02:06 PM
Edited by Nev, 06 February 2011 - 02:12 PM.
#235
Posted 07 February 2011 - 09:06 PM
#236
Posted 10 February 2011 - 08:32 AM
Alex from Pro-Alloy has emailed me to say that the Mk2 intercooler I have extracted and sent him understandably isn't intended to take 2.5 bar of boost, so I need to give him a ring today to determine what to do about this. In practice I will likely be running less than 2 bar of boost, but I'd rather get it beefed up and know I have headroom in the future to increase the boost for more power. Also, it may end up that I dump the amal valve and stick a 3rd party manual boost controller in its place. That way I can modify the boost from 1 bar to 2.5 bar depending on what the conditions are.
#237
Posted 10 February 2011 - 10:14 AM

#238
Posted 10 February 2011 - 11:19 AM
I have spoken to Alex at Pro-Alloy now and he is going to replace my 2 end caps with thicker material and replace the back plate with the hanger with thicker material. However, he didnt mention anything about welding on those reinforcing the corners with that angle alu. I might give him another call to discuss whether this is worth while on mine. He reckons these mods should probably be safe for 2 bar of boost, as Wayne is using a similar IC and so are a few others around the 2 bar mark.
I have done an 'enlarged exit pipe' airbox mod this morning, pics on the site HERE. As far as I know, nobody in the VX community has done this so far, and I think this mod would help stage 3 and 4 people as this exit pipe is a narrow constriction (64mm I/D). Its also quite an easy mod to do, took me approx 2 hours with angle grinder, dremmel, file and epoxy. If anyone wants a length of 76mm alu pipe to bond in, i can cut a length off my enormous pipe and post to you.
Edited by Nev, 10 February 2011 - 11:24 AM.
#239
Posted 10 February 2011 - 12:00 PM


#240
Posted 10 February 2011 - 12:18 PM
Quote
Have there been any quality-issues re the cc form PA?! Because I want to go down the same route. Actually I'm running 1,75 bar (roughly 26psi) of overboost with a peak of 330 bhp at 5800-6000rpm. It's the Astra VXR turbocharger I'm using.Think I was the 1st to go past the original cc spec breaking a few and even break the mk2 version so sounds like Steve has the latest beefed up version and know he has hurt a few on the way - I think a decent turbo will not cause as many issues as we see on high boost k04 7 k06/k04 setups tbh
So is there something I have to keep in mind or tell when ordering the cc from ProAlloy? A hint or something like Mk 2 or 3 chargecooler?

Please let me know! Thanks!

4 user(s) are reading this topic
0 members, 4 guests, 0 anonymous users