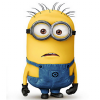
Big Power Vxt Project
#3361
Posted 17 November 2016 - 08:01 AM
#3362
Posted 17 November 2016 - 01:44 PM
Seeing your drawings I think they will add quite some backpressure; look up "Helmholts resonator" and study some high power silencer internals...
#3363
Posted 17 November 2016 - 02:38 PM
This is a good point why can't you fit a 3" tullet?Nev, please don't end up like turbo toaster lotus... burning away. Shame you can't just fit a 3" tullet..
#3364
Posted 17 November 2016 - 02:38 PM
#3365
Posted 17 November 2016 - 02:40 PM
Just keep in mind that any resonator absorber (Helmholtz, quarter lambda etc) is very frequency specific, while a porous absorber is not. Will depend on exact requirements what best to use. E.g. quiet at all frequencies/rpms or tuned to get rid of excessive noise at specific rpm. Just doing some measurements with a spectrum analyzer (guess these are available as smartphone apps) will give you a good idea what frequencies at what rpm you have to deal with. Based on that you can do an educated guess of what absorber design will work best.
Given that you don't need to get rid of 100% of the noise, just some peaks, I always wondered if a kind of noise cancellation device would work. I think I've read somewhere that you have devices that generate an exhaust sound (electric cars and such). If these are heavy duty enough, would be a relative small thing to hook them up such that they partly cancel the obnoxious frequencies.
#3366
Posted 17 November 2016 - 03:26 PM
Just keep in mind that any resonator absorber (Helmholtz, quarter lambda etc) is very frequency specific, while a porous absorber is not. Will depend on exact requirements what best to use. E.g. quiet at all frequencies/rpms or tuned to get rid of excessive noise at specific rpm. Just doing some measurements with a spectrum analyzer (guess these are available as smartphone apps) will give you a good idea what frequencies at what rpm you have to deal with. Based on that you can do an educated guess of what absorber design will work best.
Given that you don't need to get rid of 100% of the noise, just some peaks, I always wondered if a kind of noise cancellation device would work. I think I've read somewhere that you have devices that generate an exhaust sound (electric cars and such). If these are heavy duty enough, would be a relative small thing to hook them up such that they partly cancel the obnoxious frequencies.
Power requirements to produce a tone at exhaust levels will sap much more power than an over restrictive exhaust.
Best approach for a Helmholtz system is make it adjustable (trombone style) until the targeted frequencies are found.
#3367
Posted 17 November 2016 - 04:48 PM
Seeing your drawings I think they will add quite some backpressure; look up "Helmholts resonator" and study some high power silencer internals...
the new 2bular has a helmholtz resonator option
#3368
Posted 17 November 2016 - 05:00 PM
#3369
Posted 17 November 2016 - 06:34 PM
#3370
Posted 17 November 2016 - 06:47 PM
#3371
Posted 17 November 2016 - 08:32 PM
This is a good point why can't you fit a 3" tullet?Nev, please don't end up like turbo toaster lotus... burning away. Shame you can't just fit a 3" tullet..
Too noisy (they wont guarantee a set noise level), and also expensive to get them to make a bespoke system that would require me to leave the car with them.
Edited by Nev, 17 November 2016 - 08:50 PM.
#3372
Posted 17 November 2016 - 08:36 PM
Just keep in mind that any resonator absorber (Helmholtz, quarter lambda etc) is very frequency specific, while a porous absorber is not. Will depend on exact requirements what best to use. E.g. quiet at all frequencies/rpms or tuned to get rid of excessive noise at specific rpm. Just doing some measurements with a spectrum analyzer (guess these are available as smartphone apps) will give you a good idea what frequencies at what rpm you have to deal with. Based on that you can do an educated guess of what absorber design will work best.
Given that you don't need to get rid of 100% of the noise, just some peaks, I always wondered if a kind of noise cancellation device would work. I think I've read somewhere that you have devices that generate an exhaust sound (electric cars and such). If these are heavy duty enough, would be a relative small thing to hook them up such that they partly cancel the obnoxious frequencies.
Thanks Alex, I have already delved into a dynamic/adjustable resonator pipe, I have 2 locations I could fit one and test if necessary.
My "drone" freq is already measured around 95 Hz on the current exhaust. In cabin freq is different to rear of car freq BTW.
With my specific cam issue, the key noise issue is the exhaust pulses and the lumpy idle thrumming.
Edited by Nev, 17 November 2016 - 09:05 PM.
#3373
Posted 17 November 2016 - 08:40 PM
Seeing your drawings I think they will add quite some backpressure; look up "Helmholts resonator" and study some high power silencer internals...
My though flow exhaust (with open butterfly valve) will have minimal back pressure and operate very efficiently as the system will effectively be a straight line open pipe. When closed (by design) back pressure at low revs will be medium (maybe around 3 to 5 PSI at a guess from 2000 to 4000 RPM). I can increase or decrease this by changing the load on the spring.
Lastly, I am at the stage where I would be happy with any amount of back pressure really, just so I can get noise levels down.
Edited by Nev, 17 November 2016 - 09:07 PM.
#3374
Posted 17 November 2016 - 08:49 PM
I doubt very much a 3.5" exhaust is required
I agree a 3" might be "adequate" but I suspect it would rob a couple of dozen HP, maybe even 30 or 40. If you do the calcs on gas expansion and then measure the speeds it is trying to get down the exhaust pipe it doesn't take much to start approaching supersonic speeds... Even gas moving at half that speed would be far less than optimal.
Another reason I think it is of some consequence is that my power graph doesn't flatten off until 8000 RPM. There are very few 2 litre 4 pots on a small to mid framed turbo managing that.
Lastly, 3.5" is more future proof, if my turbo ever expires I will be fitting the newer Gen 2 version of the GTX3076, which makes a lot more puff (up to 750 BHP). I've come to this decision this summer when I was using the full power map and finding a shortage of power on a few occasions.
Edited by Nev, 17 November 2016 - 09:09 PM.
#3375
Posted 17 November 2016 - 08:52 PM
A full fat Dave H would solve most of the noise issues and easily accessible. I would fully recommend ceramic coating of turbo downpipe section........job done! DG
I think Dave Hardwick and Simpsons would have been the only 2 people I could trust, however the cost would have been too high (for me). Simpsons quoted me £3500 when I rang them up about 4 years ago for example. I think Dave would have had to put in extra R&D to get Nipper quiet with a 3.5" system, which inevitably (and understandably) would have been expensive.
And lastly, I want to design and build my own as I like learning and trying to do things myself (which is why I bought a £1100 welding system in the first place).
Ceramic coating is not desirable to me for quite a few of reasons:
1. If you get cracks then you can't easily re-weld the affected item. This is important as my manifold and exhaust pipes and silencers have all failed over time. If my cracked manifold had been ceramic coated then I could not have welded it a few months back (for £20). Instead I'd probably have needed a new one and new down pipe (costing circa £1000).
2. It is stupidly expensive.
3. The parts has to be posted and insured with consequential cost + risk of loss + delay meaning the car is off the road.
4. Cheap exhaust wrap works very well indeed, and only takes 1 hour to fit, abeit it disintegrates every couple of years
Edited by Nev, 17 November 2016 - 09:21 PM.
#3376
Posted 17 November 2016 - 09:16 PM
I received the sheet steel today, it looks worryingly thin to weld (1mm and 1.2mm).
The perforated sheet I bought (to make the perforated pipes) looks to be especially good. I chose 2mm diameter holes with a 3.5mm offset, meaning it has a circa 30% open surface area, and importantly loads and loads more holes than ordinary cheep eBay perforated pipe. I am hoping this will give me an advantage on sound deadening as the pulses can really dissipate into thousands of holes over the extra long stretches of pipe I have designed in.
Had a look at google analytics about the the exhaust website, average session time of people on it has been 9.5 mins so far
Edited by Nev, 17 November 2016 - 09:25 PM.
#3377
Posted 17 November 2016 - 10:26 PM
I also question the need for 3.5inch for the power your running Nev But always enjoy your journey 😊 DG
I just did the calcs again to remind us why:
Using Charles law, assuming inlet air temp = 20 degrees C, outlet from engine = 1000 degrees C, then the exhaust gas will be 4.34 times the volume.
Based on power of 520 BHP, the engine will consume circa 22000 Litres of inlet air per minute (at 20 degrees C).
So multiply 22,000 litres * 4.34 = 95,500 Litres/min coming out of the cylinders.
Push this down a 3" OD exhaust pipe with an internal X-sectional diameter of 73mm means that the gas (before taking into account temp losses) will be moving at 850 MPH.
These ball park sums (importantly) do not take into account the gas volume decrease from the cylinder to post turbo due to the cooling of the gas (probably by at least 150 degrees C). Even so, with a 3" exhaust you can see that the speed of the exhaust gas could be well over 500 MPH though. This is why 3" pipework is no good and why you hear that jet noise from under-specced exhausts on powerful cars.
Edited by Nev, 17 November 2016 - 10:37 PM.
#3378
Posted 18 November 2016 - 08:55 AM
Couple of points;
1. EGT limit is sub 1000 deg. C for conventional materials. Above that you melt valves and stretch exhaust manifold studs (and is a current limit for GDI engines running at lambda 1 across the whole map, which will have much higher EGTs). I appreciate you may well be pushing that area at certain points in your map but I suspect the reality is your map is overfuelled to bring EGT gasses down. 900 C is a much closer approximation.
2. Gas flow is laminar, so calculating bulk speed is a very poor approximation.
3rd point.
Do you actually expect post turbo/post cooler temperatures to be 20 degrees?
Edited by fezzasus, 18 November 2016 - 08:56 AM.
#3379
Posted 18 November 2016 - 10:43 AM
1. EGT limit is sub 1000 deg. C for conventional materials. Above that you melt valves and stretch exhaust manifold studs (and is a current limit for GDI engines running at lambda 1 across the whole map, which will have much higher EGTs). I appreciate you may well be pushing that area at certain points in your map but I suspect the reality is your map is overfuelled to bring EGT gasses down. 900 C is a much closer approximation.
Maybe it's 900, maybe it's 950, maybe even 1000, the number was just used for demonstration of gas speed.
2. Gas flow is laminar, so calculating bulk speed is a very poor approximation.
Yep, so the gas speeds in the centre of the bore (and outside apexes) are going to be even higher than my calcs.
3. Do you actually expect post turbo/post cooler temperatures to be 20 degrees?
I'm not sure I understand you fully, but I was assuming inlet temps into the engine were roughly 20 degrees C. Generally speaking on a cold day my boosted air is about 5 to 10 degrees warmer than ambient. The hottest I've ever seen them was 45 degrees C on a baking summer day and also 45 degrees once when doing some extended very high speed testing in Autumn.
Anyway, details aside, the outline calcs highlight the importance of > 3" pipework when you are flowing for roughly 400 BHP onwards. All my pipework on the car is larger than most people would have (inlet, outlet, runners, breathers etc). Basically the faster and easier you can get air in and out of the engine, the more power it will make. This was my fundamental mantra when doing the project, and it seems to have worked.
Edited by Nev, 18 November 2016 - 10:55 AM.
#3380
Posted 18 November 2016 - 10:54 AM
Anyway, details aside, the outline calcs highlight the importance of > 3" pipework
Well that's where the details become important. The gas expansion is the difference between the IAT and EGT, and I believe your calculations underestimate IATs and overestimate EGTs which results in a calculation overstating the volume of gas you need to flow and thus the exhaust diameter needed.
You may argue that you want to build in a safety margin but with the amount of work this safey margin involves (assuming that correct numbers allows use of a 3 inch diameter exhaust) that it would be tolerable to accept a slight loss of power on the rare occasions where these gas volume is slightly greater.
2 user(s) are reading this topic
0 members, 1 guests, 0 anonymous users
-
Bing (1)