Edited by The Batman, 23 November 2016 - 09:37 PM.
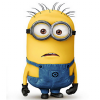
Big Power Vxt Project
#3421
Posted 23 November 2016 - 09:35 PM
#3422
Posted 23 November 2016 - 09:42 PM
I apologise I struggle to read through all the crap you write
If you don't want to read my "crap" that's fine, but then please don't ask lazy questions about it because you haven't read it.
Edited by Nev, 23 November 2016 - 09:44 PM.
#3423
Posted 23 November 2016 - 09:42 PM
#3424
Posted 23 November 2016 - 09:47 PM
#3425
Posted 23 November 2016 - 10:20 PM
Think steam ship paddle?
How would you attach the "paddle wheel" to the spindle though, so it could take the mild torque (maybe a couple of ft/lb) and also the vibrations and heat ?
Bear in mind the "paddle wheel" has to be removable.
Edited by Nev, 23 November 2016 - 10:21 PM.
#3426
Posted 23 November 2016 - 10:31 PM
That's the convention. Not sure why you've offset the butterfly axis as you won't be able to fully open
Edited by fezzasus, 23 November 2016 - 10:32 PM.
#3427
Posted 24 November 2016 - 06:03 AM
This is where it falls down as welding in the same way as the butterfly is the obvious method. You could cut the spindle into two sections, drilled down the centre, tap and fix in a similar way to a toe link bar... but the diameter of the spindle may be too small to achieve this?Bear in mind the "paddle wheel" has to be removable.
#3428
Posted 24 November 2016 - 06:10 AM

#3429
Posted 24 November 2016 - 07:11 AM
If you place the valve outside the silencer together with the 180 bend you could use one of fezz' off the shelf options.
You would loose some interior volume but you wouldn't have to worry about the spindle or getting it gas tight.
I'm following this build with great interest as I'm also planning a new exhaust for my SC this winter. Since I'm originally a bike guy I seem to try to incorporate bike solutions to my car so will probably not look like yours though. We'll see what happens
#3430
Posted 24 November 2016 - 09:07 AM
Or... another idiot idea
Cut a threat into the spindle, weld a few bolts to the "paddle", wind it onto the spindle and set the position with bolts that are also wound onto the spindle, again in a similar way to a toe link/TRE. This would also allow you to adjust it once fitted if that is required.
Yep, thanks Alex, your two ideas are virtually the same as mine at the moment:
1. cut a thread onto the spindle end for a lock nut that will secure the "paddle wheel" onto the end.
2. drill a hole in the end of the spindle for a small bolt, then square off the spindle end such that the 90 degree "paddle wheel" (also with sqare locating hole then fits onto the spindle and is held on with the tiny bolt.
Edited by Nev, 24 November 2016 - 09:14 AM.
#3431
Posted 24 November 2016 - 09:09 AM
If you place the valve outside the silencer together with the 180 bend you could use one of fezz' off the shelf options.
You would loose some interior volume but you wouldn't have to worry about the spindle or getting it gas tight.
I'm following this build with great interest as I'm also planning a new exhaust for my SC this winter. Since I'm originally a bike guy I seem to try to incorporate bike solutions to my car so will probably not look like yours though. We'll see what happens
I've seen those valves, but as you have noticed there are problems with them:
1. They have to be external to the silencer, as the spring and rubber diaphragm would fail with the heat.
2. Nobody I've seen makes one in 89mm diameter, so you can't buy one anyway.
Thanks for the kind words, I will try and measure the dB results from each step of the design, so hopefully it will give you a good clue about which of the design features works the worst/best.
Edited by Nev, 24 November 2016 - 09:19 AM.
#3432
Posted 24 November 2016 - 10:12 AM
That's the convention. Not sure why you've offset the butterfly axis as you won't be able to fully open
I'm not sure why you think the butterfly wont open fully when the pictures clearly show it does and my write up even explains the ovaloid shape to achieve this.
The spindle offset is for pressure load balancing reasons, same as on some aeroplane rudders etc.
Edited by Nev, 24 November 2016 - 10:14 AM.
#3434
Posted 24 November 2016 - 11:41 AM
https://www.ebay.com/itm/201723671660 89mm exhaust flap
Thanks, right size, but it would have to be externally mounted, also adjusting these things would require finding difference springs to have control of when exactly the diaphragm would open.
Good price too.
Edited by Nev, 24 November 2016 - 11:55 AM.
#3435
Posted 24 November 2016 - 12:41 PM
#3436
Posted 24 November 2016 - 01:44 PM
New Exhaust pipe work has been seen being shipped to Nevs address
#3437
Posted 24 November 2016 - 01:45 PM
You could connect it so a solenoid and be switch operated
On/off function isn't so good really, I'd prefer a slow ramp rate on the noise and back pressure, rather than a sudden increase/decrease.
Edited by Nev, 24 November 2016 - 02:11 PM.
#3438
Posted 24 November 2016 - 02:51 PM
Whilst sat in an IT training course, I was having a sketch as you do and can't see how th valve would open?
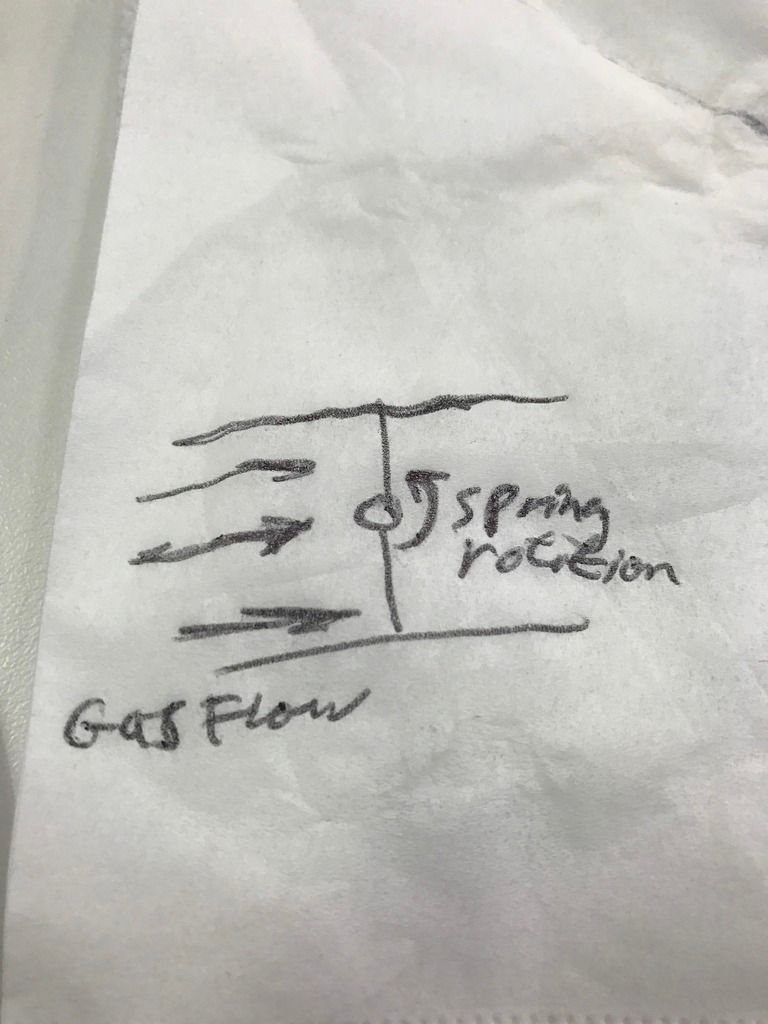
Surely the pressure at bottom of valve will try and push it open but the rest of th pressure pushing at the top of the butterfly valve will be trying to close the valve?
Hence why others use external opening forces right? Or it's quite possible that I'm missing something.
#3439
Posted 24 November 2016 - 03:16 PM
That's the convention. Not sure why you've offset the butterfly axis as you won't be able to fully open
I'm not sure why you think the butterfly wont open fully when the pictures clearly show it does and my write up even explains the ovaloid shape to achieve this.
The spindle offset is for pressure load balancing reasons, same as on some aeroplane rudders etc.
I think you'll find a central axis will be much easier to open and close, as current design has entire body of flap moving against exhaust flow, where as a central axis as equal surface area moving away from the gas as towards, meaning balanced force and lower torque input.
Additionally, your photo doesn't show the flap opening in a full length of pipe (as far as I can tell), if the length of pipe extends past the length of the flap when opened, you'll likely find it fowling
#3440
Posted 24 November 2016 - 03:34 PM
I think that is why the spindle is not in the middle. So more force opening the plate than holding it closed.So you're relying on pressure to open the valve?
Whilst sat in an IT training course, I was having a sketch as you do and can't see how th valve would open?
Surely the pressure at bottom of valve will try and push it open but the rest of th pressure pushing at the top of the butterfly valve will be trying to close the valve?
Hence why others use external opening forces right? Or it's quite possible that I'm missing something.
2 user(s) are reading this topic
0 members, 2 guests, 0 anonymous users