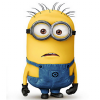
Big Power Vxt Project
#3481
Posted 01 December 2016 - 04:13 PM
#3482
Posted 01 December 2016 - 05:21 PM
I phoned dozens of engineering shops and "metal workers" to find somebody with a bead roller... absolutely nothing... each one suggested I call somebody else that they know but it was just a wild goose chase. Merlin Motorsport has one but would only roll beads into tubes that they supplied. In the end I bought my own.
Hmmm, I might have a little job for you beader soon please, can it cope with 1.5mm thickness stainless and can you position the tube so it runs the bead right on the end of the tube (ie simply flares one end of the tube, so it can slide and locate onto another tube)?
Edited by Nev, 01 December 2016 - 05:25 PM.
#3483
Posted 02 December 2016 - 10:16 AM
I wouldn't worry Nev I don't think Chris is capable of getting round a track in one piece 😂Surely you should keep your fingers off the keyboard instead of giving your company a bad reputation by presuming to infer that I (or maybe you mean the car) is either unwilling or incapable of driving round a track?
#3484
Posted 02 December 2016 - 11:05 AM
Hi Nev, you would of course be welcome to borrow it, but don't think it will meet any of your requirements... it certainly couldn't flare, and not sure it would be up to that thickness of SS.Hmmm, I might have a little job for you beader soon please, can it cope with 1.5mm thickness stainless and can you position the tube so it runs the bead right on the end of the tube (ie simply flares one end of the tube, so it can slide and locate onto another tube)?I phoned dozens of engineering shops and "metal workers" to find somebody with a bead roller... absolutely nothing... each one suggested I call somebody else that they know but it was just a wild goose chase. Merlin Motorsport has one but would only roll beads into tubes that they supplied. In the end I bought my own.
#3485
Posted 02 December 2016 - 12:08 PM
Nev, you need to search out industrial pipe laggers. its what they do.
Most of our pipework is either tinned in galv or stainless sheet over the insulation.
#3486
Posted 02 December 2016 - 02:35 PM
Nev, you need to search out industrial pipe laggers. its what they do.
Most of our pipework is either tinned in galv or stainless sheet over the insulation.
Do you mean in terms of glass fibre noise wadding or sleeve expanding or dual skinned pipes please?
I spose I should really start about thinking about buying some wadding, any suggestions from people?
Edited by Nev, 02 December 2016 - 02:39 PM.
#3488
Posted 02 December 2016 - 03:04 PM
Got my 89mm rolled tube back from the engineers this morning, am about to drive into the garage to do some flow test and a dB test on it.
(Scroll down): https://sites.google...gn/05-build-log
Edited by Nev, 02 December 2016 - 03:05 PM.
#3489
Posted 02 December 2016 - 06:05 PM
For the forming mate. They all use rollers and bead/swaging rollersDo you mean in terms of glass fibre noise wadding or sleeve expanding or dual skinned pipes please? I spose I should really start about thinking about buying some wadding, any suggestions from people?Nev, you need to search out industrial pipe laggers. its what they do. Most of our pipework is either tinned in galv or stainless sheet over the insulation.
#3490
Posted 02 December 2016 - 07:26 PM
For the forming mate. They all use rollers and bead/swaging rollers
Do you mean in terms of glass fibre noise wadding or sleeve expanding or dual skinned pipes please? I spose I should really start about thinking about buying some wadding, any suggestions from people?Nev, you need to search out industrial pipe laggers. its what they do. Most of our pipework is either tinned in galv or stainless sheet over the insulation.
Ah, gotcha, thanks for the tip.
#3491
Posted 02 December 2016 - 07:28 PM
Wow, made some nice progress today, design #1 was built and tested, noise down to about 102 dB at idle already. I'm really happy so far.
Build log here: https://sites.google...gn/05-build-log
Noise test results here: https://sites.google...6-noise-results
#3492
Posted 02 December 2016 - 07:45 PM
#3493
Posted 02 December 2016 - 08:09 PM
already have better results with the new backbox which is a good start
#3494
Posted 02 December 2016 - 08:37 PM
Respect for taking that on
#3495
Posted 02 December 2016 - 09:24 PM
Looks good, video set to private though, even for display via your website.
Works for me.
Good learning Nev.
Something you may or may not be aware of is that butterfly valves only give good flow control in the last 5% of closure. Dissappointing that the noise reduction doesn't seem that dramatic albeit that dBs are logarithmic.
#3496
Posted 02 December 2016 - 09:28 PM

#3497
Posted 03 December 2016 - 08:48 AM
Something you may or may not be aware of is that butterfly valves only give good flow control in the last 5% of closure.
Thanks, I didn't know that as a pure fact, but I was instinctively aware that the cracking open part of the valve will be more influential than the wide open part. The flap itself has 1 to 2 mm of gap all around it too (in order to stop it catching on the tube as it lifts up and down). This will allow quite some leakage.
In fact, considering the violent pulsing nature of the exhaust I am beginning to wonder if the valve is suitable, as the pulses will want to open and close it with quite some force. Yesterday when I was using my hand as a gauge around the pipe it made me realise that the spring is going to need to be at least 7 to 12 pounds just to resist the idle pressure (even taking into account the 80%:20% offset load ratio of the spindle which helps). God knows what the force might be at 6000 RPM which is where I would roughly want it to open, maybe 40 lb, which would be quite a strain on the spring assembly and very basic bearing that the spindle sits on.
I am tempted to build design #2 now (this is without the butterfly valve). This won't flow well for high RPM, but will be quieter and be less risk of failure (due to the butterfly valve failing for one reason or another).
Am having a head scratch on how to "cope" my 3 pipe joins to the tail pipe next as well as making an insert to union the flows from 2 different directions with the minimum of turbulence. Also need to buy some argon.
I should also connect up my pressure gauge to the inlet pipe stub (on the outside of the silencer) to see what the back pressure is, but I can't do this until I weld some more material on it.
Edited by Nev, 03 December 2016 - 09:15 AM.
#3498
Posted 03 December 2016 - 10:44 AM
http://www.textilete...emperature[to]=Do you mean in terms of glass fibre noise wadding or sleeve expanding or dual skinned pipes please? I spose I should really start about thinking about buying some wadding, any suggestions from people?Nev, you need to search out industrial pipe laggers. its what they do. Most of our pipework is either tinned in galv or stainless sheet over the insulation.
#3499
Posted 03 December 2016 - 01:12 PM
Built, installed and sound tested design #2 this morning; the result is another 1 to 2 dB drop when I noise tested it. It's now possible to stand behind the car with the engine idling without wincing.
It's noticeable that the "A" filter reading is dropping more than the "C" filter rating, this means the high frequencies are being reduced more than the low (bass) frequencies. As expected really.
There are a lots of rattles and wall vibrations, the bricks on top of the silencer (to hold it down) were vibrating off! This will reduce once it's all welded up firmly, especially with an intended vertical strengthening beam between the large 2 flat sections. Also some wadding will make a substantial drop in dB. Also with the box installed inside the calm will yield a mild noise drop too I expect.
All in all I am tempted to tack it together now, put some wadding in and take it for a mild drive to see what it's like when driving it.
Edited by Nev, 03 December 2016 - 01:37 PM.
#3500
Posted 03 December 2016 - 03:14 PM
TY, useful temperature ratings.
102 dB idle isn't quiet enough, so I just spent 45 mins staring into the box thinking.
I think I will experiment with a vertical column in the centre of the box to act as a 3rd perforated baffle, as per design #3.
Edited by Nev, 03 December 2016 - 03:37 PM.
3 user(s) are reading this topic
0 members, 2 guests, 0 anonymous users
-
Google (1)