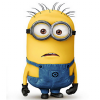
Big Power Vxt Project
#1521
Posted 25 January 2013 - 07:35 PM
#1522
Posted 25 January 2013 - 08:09 PM
#1523
Posted 25 January 2013 - 09:20 PM
#1524
Posted 26 January 2013 - 01:55 PM
If this is the case then it's virtually certain to be the seals. I've ordered a restrictor off eBay - hopefully it will fit correctly and I can actually get access to the part on top of the turbo to get it fitted.
Is your turbo a ball-bearing unit or a sleeve-bearing? Ball bearing units normally tend to need a flow restrictor to the turbo as the oil is not used (like in a sleeve-bearing) to 'float' the turbine and provide the spacing.
Sleeve bearing units should normally run such close tolerances (like main crank bearings) that they restrict flow themselves and pressure is usually not an issue.
For the return feed I'd personally have a lenght of steel pipe (perhaps attach to the turbo with a banjo bolt connection) made up to fit with a very short rubber connection on the block end to take up any thermal expansion. Turbo-block relation should be pretty much fixed anyway.. Some bracketry/webbing on the pipe to stop vibration fatigue may be needed, but it has the advantage that it can't kink ever and it's fully heat and aging resistant.. (it's what OEM's often do in these conditions.. go to hard lines..)
Bye, Arno.
#1525
Posted 26 January 2013 - 03:10 PM
#1526
Posted 26 January 2013 - 03:36 PM
#1527
Posted 26 January 2013 - 05:57 PM
For the return feed I'd personally have a lenght of steel pipe (perhaps attach to the turbo with a banjo bolt connection) made up to fit with a very short rubber connection on the block end to take up any thermal expansion. Turbo-block relation should be pretty much fixed anyway.. Some bracketry/webbing on the pipe to stop vibration fatigue may be needed, but it has the advantage that it can't kink ever and it's fully heat and aging resistant.. (it's what OEM's often do in these conditions.. go to hard lines..)
When I installed the turbo I tried to adapt the OEM metal pipe, but it wasn't possible due to the new angles caused by the new position of the turbo. I am tempted to buy a metal (brass) 135 degree or 90 degree elbow and splice it into the centre of the existing blue rubber pipe to alleviate the problem. So far today I've been too lazy to crawl under the car though !
Edited by Nev, 26 January 2013 - 06:08 PM.
#1528
Posted 26 January 2013 - 06:33 PM

#1529
Posted 26 January 2013 - 07:34 PM
I have one on order thx guys.
I think the RPM is relevant as the oil pressure is dependant on the mechanical gears of the oil pump. In my case, becuase I have spring loaded under piston jets I get a wierd scenario that it smokes upto approx 2500 RPM, then the oil pressure is enough to open the springs on the jets and suddenly drops, meaning the smoking then stops until about 4000 RPM !
The oil jets do not operate like that , they have a pressure releif valve in them so their opening is gradual, also thay are fully open at that rpm and the oil pump valve is nearly on bypass.
I would go for a maximium diameter straighter oil return pipe followed by an oil restrictor in the turbo oil feed.
Steve
#1530
Posted 26 January 2013 - 08:25 PM
For the return feed I'd personally have a lenght of steel pipe (perhaps attach to the turbo with a banjo bolt connection) made up to fit with a very short rubber connection on the block end to take up any thermal expansion. Turbo-block relation should be pretty much fixed anyway.. Some bracketry/webbing on the pipe to stop vibration fatigue may be needed, but it has the advantage that it can't kink ever and it's fully heat and aging resistant.. (it's what OEM's often do in these conditions.. go to hard lines..)
When I installed the turbo I tried to adapt the OEM metal pipe, but it wasn't possible due to the new angles caused by the new position of the turbo. I am tempted to buy a metal (brass) 135 degree or 90 degree elbow and splice it into the centre of the existing blue rubber pipe to alleviate the problem. So far today I've been too lazy to crawl under the car though !
I would remove as much rubber as possible... As/when you hit the track you'll find it doesn't last that well. I bought a steel flange from ebay and then fabricated a steel pipe with a flexi close to the block, as steve says, @ maximum diameter. Also, I would run a compression and leak down test, just in case blow-by is exacerbating your problems. If oil is moving from the turbo core to the turbine housing there has to be a pressure delta.
#1531
Posted 27 January 2013 - 07:31 AM
Edited by Nev, 27 January 2013 - 07:49 AM.
#1532
Posted 27 January 2013 - 07:53 AM
#1533
Posted 27 January 2013 - 08:26 AM
As for hitting the track, I don't think that is likely any more as my latest exhaust pipe is even noisier than the last one (just from listening to it) - very disappointing as that was it's main aim.
The standard exit from the turbo is a 5/8" (AN -10) and thus so is the current rubber pipe. Can anyone remember the thread size of the pipe end that goes into the block BTW - is it M18 x 1.5 thread?
As for compression test, hmmm, if these 2 mods don't fix it then that will be the next likely culprit, though I sincerely hope it isn't that, as the engine is only 6000 miles old.
M18 x 1.5 is correct.
I quick rolling road run with extra boost via a bleed valve without the correct fuel and ignition values would be enough to damage the pistons (melt or break the ring lands) although that is unlikley as the engine would smoke more and breath more.
Steve
#1534
Posted 27 January 2013 - 09:57 AM
#1535
Posted 27 January 2013 - 10:40 AM
#1536
Posted 27 January 2013 - 11:39 AM
#1537
Posted 27 January 2013 - 05:11 PM
#1538
Posted 27 January 2013 - 07:12 PM
#1539
Posted 02 February 2013 - 04:05 PM

Edited by Nev, 02 February 2013 - 04:25 PM.
#1540
Posted 02 February 2013 - 04:17 PM
5 user(s) are reading this topic
0 members, 5 guests, 0 anonymous users